Sustainability and The Environment
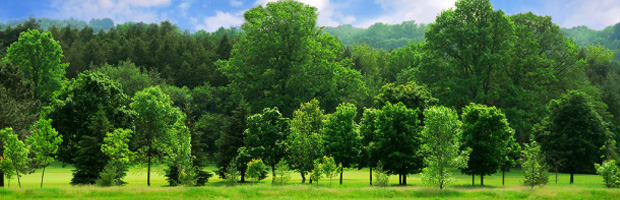
Hospital Metalcraft is committed to protecting the environment whilst continually improving its environmental performance, preventing pollution, and complying with all relevant environmental legislation, regulation and any other applicable environmental requirements.
Commitments include…
Product Re-Manufacturing, Including Re-Using Materials & Packaging Wherever Possible…
Bristol MaidTM product is designed and manufactured to minimise environmental impact throughout its lifecycle. Customers are encouraged to ‘re-manufacture’, i.e. re-use, repair & recycle wherever possible. Where this is not possible, ‘end of life’ product should be disposed of in accordance with applicable regulations, to maximise recycling opportunities. Where required, we offer a waste packaging recycling service, which ensures that your packaging is recycled effectively and responsibly, keeping you legally compliant with waste regulations and legislation.
Reducing the Volume of Waste Sent to Landfill & Reducing Waste Wherever Possible…
Following the hierarchy of prevention, re-use, recycling, energy recovery & disposal, volumes of waste consigned to landfill are minimised.
Recycling Waste Wherever Possible…
Through effective planning, waste streams are segregated to achieve regulatory compliance, optimise recycling opportunities and reduce the volume of waste consigned to landfill.
Reducing Energy Consumption…
Whilst we use green providers for our energy demands, we are continually establishing ways in which we can reduce our reliance on the national grid and increase the energy efficiency of our business…
- 1. Installation of low voltage LED lighting fitted with daylight harvesting throughout the site to minimise electrical consumption.
- 2. Use of electricity generated from our 295KW photovoltaic panel installation. Any excess is exported to the national grid.
- 3. Assessment of utility requirements during new plant & equipment procurement, to ensure that our manufacturing methods remain efficient.
- 4. Wherever possible, use of inverter controls and high efficiency motors to reduce electrical demand.
- 5. Scheduled and preventative maintenance of plant and equipment to ensure efficient operation and reduce the likelihood of breakdowns.
- 6. The re-use of energy wherever possible, i.e. warm air circulation from our compressors and paint curing oven.
- 7. The efficient generation of compressed air using specialist control systems to ensure that we only produce what is required.
- 8. The use of ultra-sonic equipment to detect compressed air leaks that would otherwise go un-noticed.
- 9. The use of high efficiency blown air and underfloor heating to minimise our gas usage.
- 10.The use of low bake paint to reduce the temperature of our curing ovens.
- 11.The use of power factor correction to optimise the efficiency of our electrical systems.
Reducing Harmful Emissions to Atmosphere…
Our delivery lorries are maintained to ensure that they run efficiently. Through the selection of Euro 6 compliant vehicles, & careful route planning we minimise emissions & travel distances. The use of our fleet on return journeys allows for effective reverse logistics. Our last financial year saw the collection of 2,284 pallets, representing a significant saving in carbon. Battery Electric cars (BEV’s), Plug-in Hybrid Electric Vehicles (PHEV’s) & Hybrid Electric Vehicles (HEV’s) are favoured over petrol & diesel equivalents. Weld fume is extracted using units fitted with high efficiency filters. The filtered air is re-circulated back inside the building. Automatic start-stop functionality ensures that the unit shuts off after a pre-determined period, saving electricity. The use of high efficiency blown air and underfloor heating minimises our gas usage, whilst low bake paints allow for a lower curing temperature. This represents a significant saving in carbon.
Reducing Harmful Content of Trade Effluent…
We only use chemicals that do not have a detrimental effect on the environment. All effluent discharged is treated & monitored to ensure that it meets acceptable levels for processing by the water authority.
Staying Compliant with Environmental Legislation…
The company maintains an Environmental Risks & Opportunities Register. Where required, this is reviewed & controls established to reduce residual risk.
Avoiding Any Pollution Incidents…
Bristol MaidTM product is designed and manufactured to minimise environmental impact throughout its lifecycle. Customers are encouraged to dispose of ‘end of life’ product in accordance with applicable regulations and to maximise recycling opportunities wherever possible.
Sustainable Sources…
Hospital Metalcraft makes sure raw materials come from sustainable sources, protecting the environment and world’s natural resources for future generations. We select FSC certified suppliers for the provision of timber-based product, i.e. paper, wood etc.
WEEE Regulations…
Hospital Metalcraft is fully compliant with the WEEE regulations and is registered as a Business to Business (B2B) Producer of electrical and electronic equipment through membership of the Veolia Environmental Services WEEE Producer Compliance Scheme, registration number WEE / KE0677RX.
Packaging Waste Regulations…
Hospital Metalcraft is fully compliant with the Producer Responsibility Obligations (Packaging Waste) Regulations and is a member of the Veolia Environmental Services Packaging Compliance Scheme, membership number 0292.
Carbon Reduction Plan…
Download our carbon reduction plan here to find out more about our initiatives and what we are doing to minimise our impacts on the environment, making for a sustainable future.